 |
News
28 Apr 2011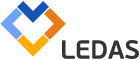
LEDAS Drastically Improves Performance of its LGS 3D Constraint SolverVersion 5.0 introduces new functions, improves speed by 30-100%
Novosibirsk, Russia: April 29, 2011 – LEDAS Ltd today announced the availability of version 5.0 of LGS 3D, its powerful geometric constraint solver. As a core technology component of CAD/CAM/CAE software, LGS 3D is used to implement geometric, dimensional, and engineering constraints in applications involving assembly design, motion simulation, and direct modeling.
Version 5.0 improves on its performance, introduces several new functions requested by LEDAS customers, and enhances the quality of its solutions.
Improved Performance
The move-under-constraints function allows users to drag one or more geometric objects interactively, while LGS 3D solves the constraints dynamically at each intermediate step. This makes it easy for users to adjust their designs, and to explore the kinematics of complex mechanisms. The new algorithm for adaptive calculation of move-under-constraints in LGS 3D 5.0 speeds up this function by 100%, on average.
LGS 3D can deal with inconsistent problems, and with version 5.0 inconsistent models are processed 30% faster on average, thanks to minimizing of the number of iterations to solve.
Extended Functions
In some design contexts, users need to know whether a particular constraint is satisfied. In previous releases, the only way to do this was to run the LGS 3D solver procedure, which proved to be time-consuming for large models. Version 5.0 introduces new functions that very quickly check if one or all constraints are satisfied.
The tangency constraint between cylinders and tori now supports the orientation attribute. Version 5.0 of LGS 3D now automatically detects the orientation attribute for coincidence constraints between circles and tori.
The distance constraint between two spheres now supports user- and application-defined help points. This allows users to measure distances between different combinations of the spheres’ sides.
Enhanced Solution Quality
The scope of some problem decomposition and heuristic methods has been extended to support models with non-rigid objects and variables.
The DOF (degrees of freedom) analysis introduced with the previous version of LGS 3D has been improved in version 5.0. The number of spiraling DOFs is minimized whenever possible.
LEDAS developers also eliminated several bugs reported by customers.
About LGS Software
Since the first commercial release in 2004, LGS 2D and 3D software components have been licensed by a dozen CAD/CAM/CAE vendors, who have embedded the components into their applications successfully.
The 2D and 3D geometric constraint solvers are used as parametric engines in applications involving 2D sketching and drawing, 3D direct modeling, assembly design, motion analysis, and other. LGS 2D and 3D are cross-platform software packages running on 32- and 64-bit versions of Windows, Linux, Mac OS X, *BSD, AIX, HP-UX, and other operating systems. Both solvers have a C-style API for easy integration into a broad range of software applications using a variety of wrappers, such as .NET, Java, and C++.
LGS 2D/3D supports the creation and modification of geometric models through explicit and implicit constraints. Points, lines, circles, ellipses, planes, cylinders, spheres, cones, tori, NURBS, application-defined parametric curves, and surfaces can be constrained. Objects can be fixed in the absolute coordinate system or relative to each other. Supported constraints include geometric relations between objects (coincidence, parallelism, tangency, and so on) and dimensions that specify the required values for distances, angles, and radii. LGS 2D/3D moves and rotates objects to positions that satisfy all constraints, yet minimizes transformations from initial configurations.
Other LGS functions implement advanced features of CAD/CAM/CAE systems, such as diagnostics of over- and under-defined parts of models, engineering variables and equations, help points, and tolerance management.
The “Lege’n’d 2D/3D” example applications are available as free downloads from the LEDAS web site. These sample models represent different kinds of 2D sketches and 3D assemblies. The applications can be used to test the functions, robustness, and performance of LGS 2D/3D. They were created with the Open CASCADE open-source application framework, and the source code is available to all licensees.
To learn more about LGS 3D, visit the LEDAS web site at www.ledas.com/products/lgs3d.
About LEDAS
LEDAS Ltd. is a private, employee-owned software development company founded in 1999. It provides constraint-based design tools, component technologies, and software development services for the CAD/CAM/CAE/PDM market.
More information about LEDAS is available at www.ledas.com.
LGS is a trademark of LEDAS Ltd. Any other trademarks are the property of their respective owners.
Press Contact
LEDAS Marketing
phone: +7 383 3356 504 / fax: +7 383 3356 256
e-mail: info@ledas.com
www.ledas.com
See also:- LEDAS distributes its infrastructure globally
- Deciding Which is Better: Plug-ins or Applications
- 3D Web, Additive Manufacturing, Kernels and Solvers Raised LEDAS Earnings in 2020
- LEDAS Signs Contracts with Billion-Dollar US Firms
- LEDAS Reports on Business Through COVID-19
- Digital Medicine Drives LEDAS 2019 Revenues 20% Higher
- LEDAS develops a lightweight Nesting module based on genetic algorithms and optimization methods
- LEDAS Rebrands with New Logo, New Web Site, New Focus
- LEDAS Celebrates 20th Anniversary with New Office
- LEDAS Cloud Platform Licensed to U.S. Dental Company Mechanodontics
- OpenBOM™ and LEDAS Announce Partnership to Help Accelerate Product Development
- LEDAS to Offer a Software Platform for Building Cloud CAD Apps
- LEDAS Contributes to Renga Software
- LEDAS Protects Customers with New Software Insurance
- LEDAS Geometry Comparison Licensed for Inventor Plug-in
- AWV and LEDAS Deliver Powerful GPU-based Tessellation Software
- LEDAS Technology Searches and Compares Big Sets of 3D Models
- Geometry Comparison From LEDAS Now Supports All Major MCAD Formats
- LEDAS Releases 3D Comparison Technology to the B2B Market
- Here's To the Quindecennial of LEDAS!
- LEDAS Labs News: Geometry Comparison Technology, Parallel Computations, Cloud Systems and Much More
- LEDAS Attracts Ever More Software Development from Global CAM Market
- LEDAS Labs Starts with Cloud-Based Geometry Comparator
- Top Systems and LEDAS Present Brand New Geometric Kernel RGK at COFES Russia 2013
- OR Laser and LEDAS Sign Long-term Service and Consulting Agreement
- RGK Russian Geometric Kernel Celebrates First Full-Featured Version
- LEDAS Establishes US Business Entity to Better Serve Clients Worldwide
- Cooperation between ASCON, Bricsys and LEDAS Brings Variational Direct Modeling to KOMPAS-3D
- Software Developer LEDAS Sets Second Consecutive Revenue Record
- LEDAS to Distribute ASCON’s C3D Modeling Kernel Internationally
- LEDAS Experts: How our Company is Involved in Developing Russian Geometric Kernel
- Russian National 3D Kernel
- LEDAS Assists STANKIN to Develop a New 3D Modeling Kernel
- LEDAS Implements Variational Direct Modeling in KOMPAS-3D
- LEDAS Appoints Alexey Ershov as New CEO
- LEDAS Achieves Record Revenues from Its Portfolio of Software Development Services
- From the Prague Spring to a Siberian summer
- New Armor for Rhino
- Get back! (Personal Impressions from COFES-2011)
- RhinoWorks from LEDAS Revolutionizes Direct Modeling
- LEDAS Adds Profile Management to LGS 2D Constraint Solver
- LEDAS Changes Leadership to Better Guide Future Development of CAD Technology
- LEDAS Appoints Dmitry Ushakov as New CEO
- Innovations Should be More Practical, Less Political. COFES-Israel Forum Report
- LEDAS Improves Google SketchUp 8 with Driving Dimensions 1.4
- Cimatron to Introduce New Motion Simulator Powered by LEDAS LGS 3D
- LEDAS Releases LGS 3D v4 Constraint Solver for Assembly Design and Direct Modeling
- LEDAS Improves Variational Direct Modeling with RhinoDirect 0.4
- LEDAS Releases LGS 2D v5 Constraint Solver with Extended Functions
- LEDAS Enhances 3D Geometry Editing for RhinoDirect Beta 0.3
- LEDAS OpenCASCADE Application Development experience: Computer-Aided Design Solutions, R&D, Variational Direct Modeling Technology
- LEDAS made Constraints Demo Application available for all ODA members
- LEDAS Adds Advanced Parametric Drawing Functions to Version 4.0 of its 2D Constraint Solver
- LEDAS Releases Driving Dimensions v.1.3 for Google SketchUp
- LEDAS Adds Movie Recording and Localization to RhinoAssembly
- How To Make a 3D Cartoon in Rhino: A Practical Guide
- LEDAS Ships LGS 3D v3 for Variational Direct Modeling Developers
- Open Design Alliance and LEDAS Implement Parametric Drawing Tools Compatible with the DWG 2010 file format
- LEDAS Announces RhinoDirect 0.1
- University of Michigan Taubman College Licenses Academic Version of LGD 3D Geometric Constraint Solver by LEDAS
- LEDAS Enhances Parametric Drawings with Updated 2D Geometric Constraint Solver
- LEDAS Improves Parametric Design in SketchUp
- How to Express Design Intent in Rhino 3D
- LEDAS Ships Next Generation of 3D Geometric Constraint Solver
- LEDAS Adds Assemblies and Kinematics to Rhino
- LEDAS Geometric Constraint Solver LGS 3D Is Licensed By Joe Gibbs Racing
- LEDAS Improves Assembly Design and Kinematic Simulation in Rhino 3D and Announces History-Free Geometry Editing
- LEDAS Supports Research on Future CAD at Purdue University
- SketchUcation.com published an interview with Dmitry Ushakov about Driving Dimensions Plugin
- LEDAS Ports its Driving Dimensions plugin for Google SketchUp to Mac and Reports 10,000 Downloads of Windows Version
- ODA and LEDAS to Cooperate in the Development of Geometric and Dimensional Constraints in DWGdirect
- LEDAS Announces Beta Release of Driving Dimensions Plugin for Rhino
- COFES – Wish you were here
- The prodigal son of Autodesk
- LEDAS Announces Availability of its Variational Geometric Solver LGS for the Mac
- CD-adapco licenses LEDAS variational geometric solver LGS 2D
- LEDAS Celebrates its 10th Anniversary While Becoming Closer to CAD Users
- LEDAS Takes 3D History-Free Parametric Design to the Next Level by Releasing Driving Dimensions 1.0 Plugin for Google SketchUp
- LEDAS Opens Driving Dimensions Labs
- LEDAS Improves Variational Sketching Usability with Release 2.2 of its LGS 2D Geometric Solver
- LEDAS Helps CAD/CAM/CAE Developers Efficiently Model Large Assemblies with LGS 3D Geometric Solver Version 1.5
- Driving Dimensions for Google SketchUp Public Beta Downloads Top 3,000 in Three Months
- LEDAS expands capabilities of free parameterization in Google SketchUp
- VirtualCAD and LEDAS provide ROCOM with parametric on-line parts catalog
- LEDAS announced successful completion of the first stage of the project for localizing DELMIA solutions for the Russian market, commissioned by Dassault Systèmes
- LEDAS opens up parametric modeling for Google SketchUp users
- LEDAS is bringing the new technology of variational direct modeling to the market
- Variational Direct Modeling: How to Keep Design Intent in History-Free CAD
- LEDAS increases the productivity of LGS 2D variational geometric solver
- Common Pitfalls in Parametric CAD Systems
- LEDAS releases 64-bit version of its variational geometric solver
- Using LEDAS Computational Software Toolkits to Shorten Development Cycle of Variational CAD Systems
- LEDAS published first ever PLM Encyclopedia
- LEDAS announces successful Third isicad Forum «PLM+ERP: Informational Environment of a Modern Enterprise»
- LEDAS releases new version of its variational geometric solver LGS 3D
- LEDAS license Academic version of geometric solvers LGS 2D/3D to Northwestern Politechnical University, China
- LEDAS delivers ENOVIA SmarTeam in Russian for Dassault Systèmes
- LEDAS to release first ever PLM+ERP Encyclopedia on isicad-2008 conference.
- LEDAS on-line solutions simplify parametric CAD trainings.
- LEDAS extends its business by developing parametric parts libraries
- Swiss AWV Company succeeds with LEDAS geometric solvers
Permanent link :: http://isicad.net/news.php?news=14400
|
 |