 |
Articles
3 Apr 2012 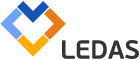
Russian National 3D KernelDmitry Ushakov Computer-Aided Drafting systems were created in the 1960s to replace “Kuhlmann” drawing boards (traditional drawing tools used by architects and engineers around the world after the industrial revolution of XVIII c.). Today, from a routine automation aids, Computer-Aided Drafting has evolved into a key instrument for innovations in various sectors of industry - Computer-Aided Design systems.
Instead of drawing floor layouts and facades, modern architects use CAD to develop informational (3D) models of buildings. Interior designers discuss the appearance of an office or an apartment with a client, moving across its virtual 3D model, integrated into the environment of a real building. An artist can create sketches on complex 3D surfaces rather than sheets of paper. An industrial designer prints a ready model on a 3D printer and forwards it to an expert on ergonomics for further analysis. In a matter of seconds, a design engineer is able to localize and modify a troubled block in an assembly comprising hundreds thousands components, which was identified as a result of automated simulation of product behavior under load. A planning engineer can promptly put together an error-free control program for an NC machine, to be able to cut out from an unfinished product a piece with a very complex surface geometry, ideally designed to have the required functional qualities. A worker responsible for product assembly and servicing uses a 3D model as a reference –to view a demonstration of a particular operation at the required angle and approximation. This is just a small part of the tasks that today can be solved with CAD. 3D models play the key role here.
3D modeling and Virtual Reality
As far back as in the 1970s scientists from all over the world, working jointly with representatives of the military and industries, began to study various methods of representing 3D data on computer, to make subsequent work with them easier. Until recently 3D models existed only in the heads of designers, which generated numerous problems and errors – both in product design, and manufacturing, operation and disposal. Experience of the leading companies, accumulated in the recent years, shows that using 3D digital models of the products through all stages of the product life cycle reduces design costs, accelerates product launch, makes manufacturing less expensive, and enables to promptly introduce changes, suggested by users, to the product design and reduce harmful effects to the environment to the necessary minimum. Ultimately, 3D modeling significantly increases competitive ability of a company and its ability to react quickly to any developments in the economy.
By now 3D modeling has over than 30-year history. By no means all ideas turned to be productive. By no means all companies that develop tools for 3D modeling managed to survive market turmoil. The best experience, however, seems to be accumulated for software components called 3D modeling kernels, which now form the basis of practically any CAD (as well as CAE and CAM) application. Developers of engineering software either design, code and independently support such components, or license them from third-party component providers. 3D-kernel forms the foundation of the “building” of any modern CAD. Everything else depends on this foundation – capabilities of various tools, their speed performance, fault tolerance, and even overall system intelligence.
From the viewpoint of a programmer, geometric kernel is a library of functions / classes that models geometric objects (a point/interval/arc/curve, a piece of surface, a solid body), changing their shapes and sizes, creating new objects on their basis, visualizing a model on a computer screen and exchanging 3D data with other programs. The list of kernel functions can be squeezed in a single sentence, but their implementation is stretched out for dozens and even hundreds man-years. The thing is that behind every elementary operation (like crossing two NURBS surfaces) there is a computational algorithm, implementing and adjusting which is a rather labor-intensive task, requiring immaculate mastering of the instruments of computational mathematics as well as professional knowledge of a particular subject. A kernel has hundreds of such operations (if we take into account huge diversity of the types of geometric data).
NURBS – the most common representation of 3D geometry
Not all CAD developers (the more so CAE and CAM) are prepared to make such considerable investments in the basic technology, so majority prefer to license a ready 3D-kernel from third-party vendors (sometimes from their direct competitors), making regular payments to the company that developed a kernel (typically, a specific sum from each sold copy of an end- product). In return they are able to use a kernel that has already been tried in other systems and, therefore, has rich functionality and is highly reliable. Finally, by getting a ready kernel, a CAD developer will be able to launch its software product quicker. Sometimes, this the factor is the dominant one – if a company is late releasing a product for a year or two, the market can become occupied by the competitors. A striking example is MCAD (Mechanical CAD) system SolidWorks, which was the first system of parametric solid modeling for Windows in the world and still is the absolute leader in MCAD by the number of sold licenses. The same avenue later was explored by developers of many other successful systems, including Russian companies ADEM and Top Systems.
T-FLEX CAD by Top Systems (Russia) based on Parasolid 3D kernel by Siemens (Germany)
Nevertheless, in the CAD world there are few companies that focus on a possibility to achieve full control over the source code, prompt error correction and building-up functionalities, fast transfer to new platforms, and, therefore, are prepared to use their own resources to achieve this. The group comprises the four leaders of the CAD market, whose revenues are running into billions (Dassault, Autodesk, Siemens and PTC), as well as few smaller companies (including ASCON, a leading Russian CAD vendor).
KOMPAS-3D by Ascon based on its own 3D kernel
In the Table below you can see a representative list of developers that belong to both categories.
Software
|
Vendor
|
Domain
|
3D-kernel
|
4MCAD IntelliCAD
|
4M S.A., Greece
|
CAD, AEC
|
Open CASCADE Technology
|
Adams
|
MSC Software, USA
|
CAE
|
Parasolid
|
ADEM
|
ADEM, Russia-Israel-Germany
|
CAD, CAM, CAPP
|
ACIS
|
ADINA Modeler
|
ADINA R&D Inc., USA
|
CAE
|
Parasolid & Open CASCADE Technology
|
Alibre Design
|
3D Systems, USA
|
MCAD
|
ACIS
|
Allplan
|
Nemetschek AG, Germany
|
AEC/BIM
|
SMLib
|
AMPSolid
|
AMPS Technologies, USA
|
CAE
|
ACIS
|
ANSYS
|
ANSYS Inc., USA
|
CAE
|
ACIS & Parasolid
|
APM Studio
|
ÍÒÖ ÀÏÌ, Russia
|
MCAD
|
Own kernel (APM Engine)
|
ArchiCAD
|
Graphisoft, Hungary
|
AEC/BIM
|
Own kernel
|
ARES
|
Graebert, Germany
|
CAD
|
ACIS
|
Ashlar-Vellum Cobalt, Xenon, Argon
|
Ashlar-Vellum, USA
|
MCAD
|
ACIS
|
AutoCAD
|
Autodesk, USA
|
CAD, AEC, GIS
|
Own kernel (ASM)
compatible with ACIS
|
Autodesk Inventor
|
Autodesk, USA
|
MCAD
|
Own kernel (ASM) compatible with ACIS
|
Autodesk Moldflow
|
Autodesk, USA
|
CAE
|
Parasolid
|
Autodesk Revit Architecture
|
Autodesk, USA
|
AEC/BIM
|
Own kernel (ASM) compatible with ACIS
|
bonzai3d
|
AutoDesSys, USA
|
CAD
|
own kernel + ACIS
|
Bricscad
|
Bricsys NV, Belgium
|
AEC, MCAD
|
ACIS
|
BtoCAD
|
YuanFang Software Co., Ltd., China
|
CAD
|
ACIS
|
CADopia
|
CADopia Inc., USA
|
CAD
|
ACIS
|
CATIA
|
Dassault Systemes, France
|
CAD/CAM/CAE, AEC
|
CGM
|
Cimatron
|
Cimatron Limited, Israel
|
CAM
|
ACIS
|
CollabCAD
|
National Informatics Centre, India
|
CAD/CAM
|
Open CASCADE Technology
|
Creo (former Pro/Engineer)
|
Parametric Technology, USA
|
MCAD
|
GRANITE
|
Creo Elements/Direct Modeling (former CoCreate)
|
Parametric Technology, USA
|
CAD
|
ACIS
|
Edgecam
|
Planit Software, UK
|
CAM
|
Parasolid & GRANITE
|
ESPRIT
|
DP Technology Corp., USA
|
CAM
|
Parasolid
|
form-Z
|
AutoDesSys, USA
|
CAD
|
own kernel + ACIS
|
FreeCAD
|
Open project
|
CAD
|
Open CASCADE Technology
|
GibbsCAM
|
Cimatron, Israel
|
CAD/CAM
|
Parasolid & GRANITE
|
GstarCAD
|
Suzhou Gstarsoft Co., Ltd, China
|
CAD
|
ACIS
|
IRONCAD
|
IronCAD LLC, USA
|
MCAD
|
ACIS & Parasolid
|
KeyCreator
|
Kubotek USA Inc., Japan-USA
|
CAD
|
ACIS
|
KOMPAS-3D
|
ASCON, Russia
|
MCAD, AEC
|
Own kernel
|
Mastercam
|
CNC Software, USA
|
CAD/CAM
|
ACIS
|
Masterwork
|
Tecnos G.A., Italy
|
CAM
|
Open CASCADE Technology
|
MicroStation
|
Bentley Systems, USA
|
AEC
|
Parasolid (previous versions used ACIS)
|
Moment of Inspiration
|
Triple Squid Software Design, USA
|
CAD
|
SOLIDS++
|
NX
|
Siemens PLM Software, Germany-USA
|
CAD/CAM/CAE
|
Parasolid
|
Patran
|
MSC Software, USA
|
CAE
|
Parasolid
|
Power NURBS
|
Ideate Inc., USA
|
CAD
|
SOLIDS++
|
PowerSHAPE
|
Delcam plc, UK
|
CAD/CAM
|
Parasolid
|
progeCAD
|
progeCAD Srl Uninominale, Italy
|
CAD
|
ACIS
|
Radan
|
Planit, UK
|
CAD/CAM
|
ACIS
|
Rhinoceros
|
Robert McNeel and Associates, USA
|
CAD
|
SOLIDS++ (particular modules)
|
Shark LT
|
Encore, USA
|
CAD
|
ACIS
|
SmartCAM
|
SmartCAMcnc, USA
|
CAM
|
ACIS
|
Solid Edge
|
Siemens PLM Software, Germany-USA
|
MCAD
|
Parasolid (previous versions used ACIS)
|
SolidWorks
|
Dassault Systemes, France-USA
|
MCAD
|
Parasolid
|
SpaceClaim
|
SpaceClaim Corp., USA
|
MCAD
|
ACIS
|
STAR-CCM+
|
CD-adapco, UK-USA
|
CAE
|
Parasolid
|
StruCad
|
AceCad Software, UK
|
AEC/BIM
|
Own kernel
|
T-FLEX
|
Top Systems, Russia
|
MCAD
|
Parasolid
|
ThinkDesign
|
Versata, USA
|
MCAD
|
Own kernel
|
TopSolid
|
Missler Software, France
|
CAD/CAM
|
Parasolid
|
TurboCAD
|
IMSI/design, USA
|
AEC, MCAD
|
ACIS
|
Vectorworks
|
Nemetschek, Germany
|
AEC
|
Parasolid (previous versions used SMLib)
|
ViaCAD 2D/3D
|
Encore, USA
|
CAD
|
ACIS
|
ZW3D (former VX CAD/CAM)
|
ZWCAD Software, China
|
MCAD
|
Own kernel (VX Overdrive)
|
ZWCAD
|
ZWCAD Software, China
|
CAD
|
ACIS
|
As you can see from the Table, the most actively licensed kernels are ACIS (developed and supported by Spatial, a subsidiary of Dassault Systemes) and Parasolid (Siemens PLM Software). Soon, however, there will be a new player on the market of 3D-kernels.
Since 2007 the Government of the Russian Federation has been carrying out the “National Technological Base” Federal Special Program aimed at creating new state-of-the-art technologies and equipment, introducing the newly developed technologies in production, commercializing new technologies, laying down the groundwork in science and technology for developing advanced science-intensive products, and improving environmental conditions in Russia. Under the framework of the Program, the Ministry of Industry and Trade and of the Russian Federation announced a tender for research and development works on “Developing Russian Licensable Software – a Mathematical Kernel for 3D-Modeling as a Basis of Computer Systems for Computer-Aided Design of Complex Engineering Products”. As a basis of a new generation of computer systems for design, reverse engineering, production planning and drawing technical documentation, this kernel will facilitate development of innovative products by Russian industries, which will be competitive on the global market, becoming a part of the national engineering capability. The tender was won by “STANKIN” Moscow State Technological University – a Federal State Budgetary Educational Institution of Higher Professional Education, and LEDAS became one of subcontractors.
LEDAS was chosen because it has thirteen years of experience in developing key software components for CAD, including projects it carried out for global leaders in the engineering software market. The projects included the development of an interval mathematical solver used in end-user tools for knowledge-based engineering; creating a geometric constraint solver and its application to parametric drafting, assembly design, animation, kinematics analysis, and direct modeling; establishing methods for converting polygonal meshes into subdivision surfaces, and the unfolding of 3D meshes on planes; calculating distances between 3D objects and performing real-time collision detection; developing feature-based CAD data translation.
No doubts, developing a new 3D-kernel it is important to rely of on predecessors’ experience to adopt their best achievements and avoid their mistakes. Therefore, in the forthcoming publications we plan to highlight a brief history of the previous attempts to create 3D modeling kernels and explain what will be different in a new Russian kernel.
Permanent link :: http://isicad.net/articles.php?article_num=15189
|
 |