 |
Articles
15 Jul 2011 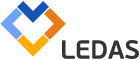
New Armor for RhinoDmitry Ushakov New Capabilities of Rhino 3D Demonstrated in London at Rhino UK User Meeting 2011
A quarter of a century ago an American Robert McNeel, an accountant by education, founded a new company in Seattle - Robert McNeel & Associates (RMA), which became one of the first resellers of AutoCAD. Popularity of this drawing system was growing, and ahead of everybody else Bob realized the prospects of 3D modeling based on a sophisticated functional of free-form surfaces. RMA started developing a corresponding plug-in for AutoCAD at the beginning of the 1990s, when such applications for PC simply did not exist. (SolidWorks, the first 3D CAD for Windows, was developed later and its capabilities for work with free-form surfaces were and remain extremely limited.) In 1998 RMA launched an absolutely unique product - Rhinoceros 1.0. Working on the project, Bob and his team rejected the idea to create a plug-in for AutoCAD and developed a new product from scratch. Its technological basis - openNURBS library – was published as an open source, which enabled anyone to get full access to recording / reading / modifying geometric data and cleared the way to broad integration of Rhino with other CAD and development of numerous plug-ins (currently – over than 200), created by RMA, as well as other developers. Most importantly, Rhinoceros capabilities for modeling free-form surfaces have remained unrivalled in this price niche (in the US the price of single Rhinoceros license is less than a thousand dollars). Today similar modeling functions can only be provided in much more expensive systems (CATIA, Alias).
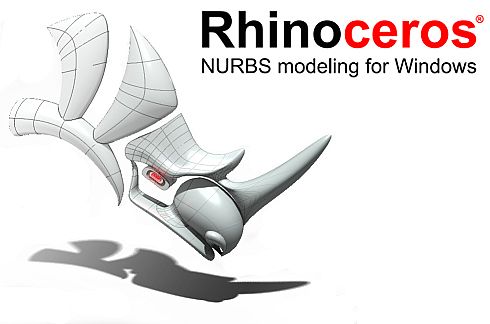
Not surprisingly, Rhinoceros promptly gained popularity in the niche of industrial design, marine design, design of interiors, furniture items, jewelry – in all areas that require work with complex-form products and where typical users are individual designers or small teams, for whom it does not pay to buy high-end CAD licenses (intended primarily for car-manufacturing and aviation industries). Interestingly, RMA managed to occupy this niche without additional “noise” – the company has never pursued an active marketing policy, focusing instead on promoting their product by the users, many of whom later became Rhino resellers.
A British company Simply Rhino Limited is the most successful Rhinoceros reseller in Europe. I think that to a considerable extend their achievements are due to the company’s location – London is a recognized design and architectural centre of the world. Simply Rhino Limited is so successful that it can afford to organize Rhino UK User Meeting 2011, which was held in London in the Design Museum (where else it could be?!) on July 6, 2011.
As RMA does not organize user conferences by itself, any Rhino-event automatically becomes global, attracting attention of users, developers and resellers from all over the world. This time was not different. Only four plug-in developers were given a possibility to make presentations at the conference. And it’s pretty flattering that one of these companies is LEDAS of Novosibirsk, Russia, of which I am a CEO (three others are T-Splines and Intact Solutions from the USA and a German Virtual Shape Research).
For many years LEDAS has been known to the CAD/CAM community as a supplier of services and technologies on the market of science-intensive programming: since 1999 we have been working for Dassault Systemes, Exigen, Cimatron and other companies, developing for them computational libraries to solve complex tasks of resource scheduling, parametric optimization, knowledge engineering, constraint solving, collision detection, motion simulation, etc. In 2009 LEDAS for the first time entered the market of end-user software, announcing development of Driving Dimensions parametric plug-ins for SketchUp and Rhinoceros. Both plug-ins caused considerable reaction in the users communities: thanks to our plug-ins popular 3D modeling systems are transferred in full-fledged parametric CAD that not only are able to create geometric models but also modify them in a convenient manner. Recently LEDAS has considerably extended the plug-in functionality for Rhino, and - simultaneously with launching a new 2.0 version, it was given a new name - RhinoWorks to reflect a broad range of its capabilities: from parametric modification of simple geometric features(pads, pockets, holes, fillets) and smart editing of imported geometry with automatic design intent recognition to bottom-up assembly design with use of mates and driving dimensions, solving direct and inverse kinematics tasks - up to and including high-quality 3D animations of moving mechanisms:
Unfortunately, growing popularity of this plug-in is hampered by entrenched prejudices that parametric design is something rather complex, available only in expensive systems that require preparatory training and – the most important – ultimately making modifications of complex geometrics more difficult. This is correct if we have in mind history-based parametric design, where changing parameters means regenerating geometry and repeating all operations employed to create a model. Obviously, a tree of a somehow non-trivial model is absolutely immense, and probabilities to find the exact parameter, which you need to modify in a particular moment, are directly proportional to the experience and clear-sightedness of the user who created the model.
Rhino users already had a chance to enjoy parametric design based on model regeneration. The most known product in this field is Grasshopper plug-in, developed and (at the moment) distributed free-of-charge by RMA. Few enthusiastic users mastered this design technique and undoubtedly admire its power. However, even they agree that it is not very easy to persuade inexperienced Rhino users to try this plug-in. At Rhino UK User Meeting 2011, Gerard Petersen, the CEO of RhinoCentre (The Netherlands), demonstrated an impressive yacht model he had created personally. The model was based on a Grasshopper diagram and Gerard acidly pointed out: "Italians should like it", making a hint about obvious associations of the diagram with a hearty portion of spaghetti.
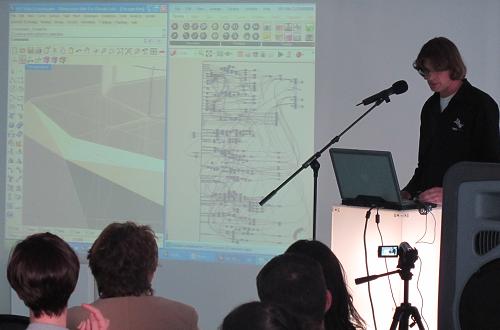
Certainly, spaghetti should be tasty (especially when cooked by an Italian), but imagine that you must find a single piece of spaghetti in your plate (or even in the whole pot) and identify the position, where the required parameter is located. Besides, there is high probability that the required parameter is absent – unless the “cook” who prepared the “dish” really put it there.
And what can be done if the model was formed without Grasshopper or simply imported to Rhino from another system (for instance, SolidWorks)? Refuse to complete parametric identification? Luckily, all such problems can be solved by rejecting tree derivation in favor of a constraint set. A constraint is an entity that determines the shape and relative position of the elements of a model. For solid and surface 3D models such elements can be faces, edges and verteces on their boundary. Various constraints can be specified between the elements: coincidence, parallel or perpendicular alignment, tangency, the given distance and angle. For edges in the form of a circlular arc and faces that are part of spherical, cylindrical and toroidal surfaces, it is also possible to specify radius and concentricity constraints. The given constraints affect geometric forms of your model and help position geometric features and assembly parts. It is essential that RhinoWorks plug-in can recognize your design intent by identifying many constraints automatically (coincidence, parallel alignment, equality of radii, etc.), so you do not need to specify them manually. Typically, you only need to specify a few driving dimensions required to modify the model the way you need. Then the given constraints (together with the automatically recognized ones) are solved by a highly productive geometric constraint solver (a unique LEDAS solution available for licensing to third parties), and all changes to the model are local and do not require expensive model regeneration from scratch. Another important aspect is that (unlike the history tree) you can add constraints to any existing model, including models imported to Rhino from other CAD system. The main advantages of the parameterization approach used in RhinoWorks plug-in are obvious: simplicity, power, universality.
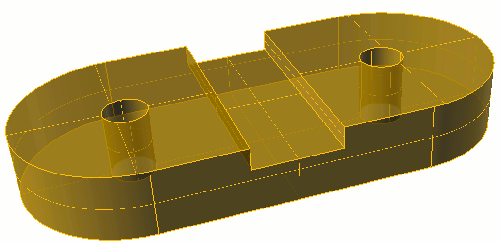
I told all this to 150 attendees of Rhino UK User Meeting 2011, accompanying my presentation by a vivid demonstration of how the plug-in works and using examples with editing parametrically simple geometric features and a complex part imported from SolidWorks, as well as simulating the motion of a manufacturing robot. The day before, taking an opportunity of another invitation, kindly offered by Paul Cowell (the CEO of Simply Rhino), I made a similar presentation at a London architect bureau - Zaha Hadid Architects for around 50 Rhino users. Both presentations raised considerable interest of the audience: I was asked multiple questions about plug-in capabilities and LEDAS plans to further advance the plug-in. Users passionately approved of all functions planned by LEDAS: variable dimensions and equations, dimension control through Microsoft Excel tables, grouping constraints in folders, diagnostics of absence of mutual interference of the mechanism details, etc. Many attendees decided to buy the plug-in right away (Simply Rhino, the exclusive reseller of RhinoWorks in the UK, received several plug-in orders).
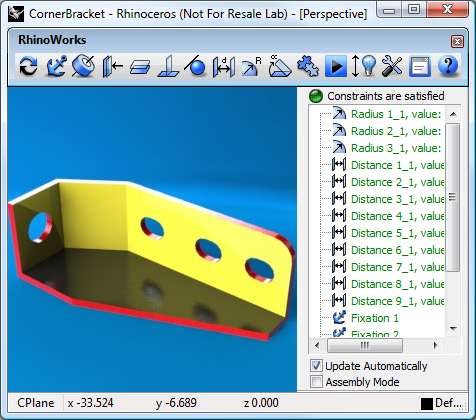
Rhino UK User Meeting 2011 started with a report by Carlos Perez, the Head of the European office of RMA in Barcelona. Carlos said that in 13 years since releasing the first version of Rhinoceros, the number of legal user sites have reached 300,000 installations (it is not possible to count the number of illegal users but it must be at least five times higher). Industrial design remains the major market for Rhino; however, recently the highest increase of the number of users has been gained through architect bureaus. The Rhino system is installed in 10,000 educational institutions throughout the world. The total number of registered developers has reached 12,000. Since the 4th version was released in 2007, sales of commercial licenses have grown by 200%, and educational licenses – by 400%. RhinoFabLab, a new social network was recently launched for Rhino users.
The major portion of his presentation Carlos devoted to description of novelties in Rhino V5 – a long-awaited new version of the system. The exact release data is not given yet but it is known that the new release is simply a matter of months. Enthusiastic users can already try a beta version of Rhino 5 WIP (“work in progress”). 32- and 64-bit Windows-versions are available, and a version for Mac OS X is on its way. Automatic customization in the new version will be achieved using Rhino.Python as a scripting language. Scripts in this language will be identically performed on all supported platforms.
The 5th version will finally have a single control centre for the installed plug-ins, including license control (currently each plug-in developer provides its own license model and its own installer). Also RMA will continue developing iRhino 3D – a 3D model viewer in a 3DM format for iPhone/iPad.
In London Carlos Perez demonstrated some capabilities of Rhino V5 live: real-time photorealistic rendering, editing solid bodies by direct deformation of their faces using a new command - PointOn, SketchUp-style dragging of body faces, etc.
Matt Sederberg, CEO and founder of T-Splines, a company that promotes advanced tools for organic surface modeling, gave a detailed account of novelties in a recently released 3rd version of T-Splines for Rhino. At this point a discriminating reader can ask a question: why Rhino users need special organic surfaces modeling if embedded tools can create NURBS-surfaces of any complexity? The thing is that classical NURBS-surfaces cannot give the required degree of smoothness and visual beauty at the points where faces adjoin. It is especially important for modeling organic objects, which Matt demonstrated with two versions of Gollum (a fantasy character from a film “The Lord of the Rings” by Peter Jackson): first was made with NURBS, and second was based on subdivision surfaces (the technology behind T-Splines). The difference, visible to the naked eye, at some point forced WETA studio to completely remodel the character (initially completed in NURBS) with subdivision technology. Most of his presentation, Matt focused on the new features of the 3rd plug-in version.
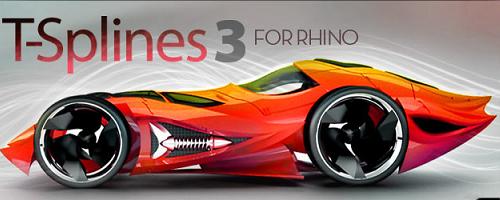
Professor Vadim Shapiro, from University of Wisconsin-Madison, developed a unique method of finite element analysis that does not require definition of an explicit finite element mesh (it is implicitly computed in course of calculations – directly based on a geometric body form). To commercialize this method of engineering analysis, a new company - Intact Solutions was formed, which has recently released Scan&Solve plug-in for static express-analysis of load stress and deformation under load directly in Rhino. In his presentation Vadim showed several interesting models (a designer chair designed with the help of T-Splines, a cathedral, a machine-building component, the Statue of David reconstructed from a digital scan). A distinctive feature of Scan&Solve is that there is no need to remove small details from a model (like 3d-inscriptions) before completing analysis. Here SolidWorks requires users to work manually, while Scan&Solve users do not need this at all!
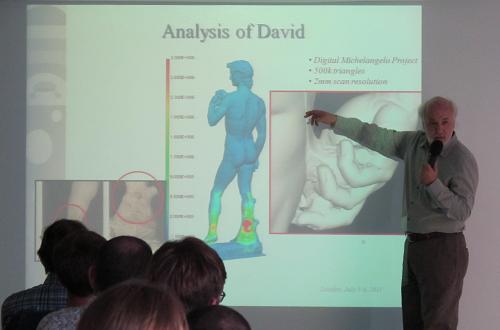
Peter Salzmann told about the products of VSR (Virtual Shape Research) from Germany. The company was founded by former ICEM employees, who did not wish to work for Dassault Systemes following a recent acquisition. By now VSR has already released two plug-ins: VSR Renderer (for real-time photorealistic rendering) and VSR Shape Analysis (that helps find geometric errors in a model). At the User Meeting, Peter announced a forthcoming release of the third product: VSR Shape Modeling, to which he devoted the major part of his presentation. The new plug-in offers convenient interactive editing of free-form surfaces. It is possible to create a surface upon an array of cells, being able to control the degree of surface smoothness in each points, move them to change the surface form interactively, smoothly connect two pieces of surfaces, etc. There is an interesting possibility to create rectangular surface patches upon selected areas of a polygonal mesh (enabling prompt and convenient transformation of a mesh model into NURBS).
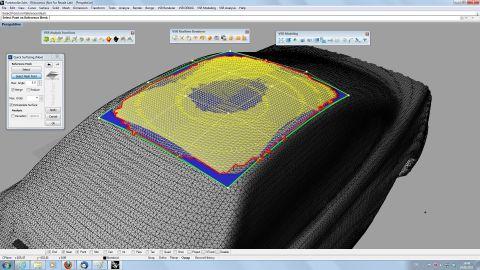
Wrapping up his presentation, Peter demonstrated impressive real-time rendering capabilities. Interestingly, there is a convenient full-screen mode that allows switching between different variants of the same model. It is important that the plug-in knows how to simultaneously load all processor cores, employing computational resources to the full.
Along with plug-in developers, Paul Cowell invited experienced Rhino users – representatives of the best design studios to take part in the Meeting. They gave remarkable examples of Rhino use and explained how those were created. For instance, already mentioned Gerard Petersen spent years to achieve his project. Gerard designs yachts. At the beginning he drew them on paper and then he began using Rhino 1.0 and mastered all subsequent Rhino versions as they were released. In 2001 he finally managed to create a complete 3D boat model entirely in Rhino. At the same time, he became a Rhino reseller upon a proposal of Bob McNeel. Gerard showed fascinating yacht models he designed in Rhino and shared several observations with the audience. Apparently, navigating a 3D model (a virtual yacht tour) seems to be the main driving sales force – a customer immediately places an order as soon as he sees the interior of his future yacht. BTW, to navigate a 3D model, Gerard used a Space Navigator 3D mouse developed by 3DConnexion. Overall, according to Gerard, the future of Rhino is in integrated design. It is time for the system to get away from the narrow niches of conceptual design, visualization, etc., and be the centerpiece of engineering process. True: what Gerard is able to create using Rhino can already be called approximation to a digital mock-up, which is a well-known concept in machine-building design.
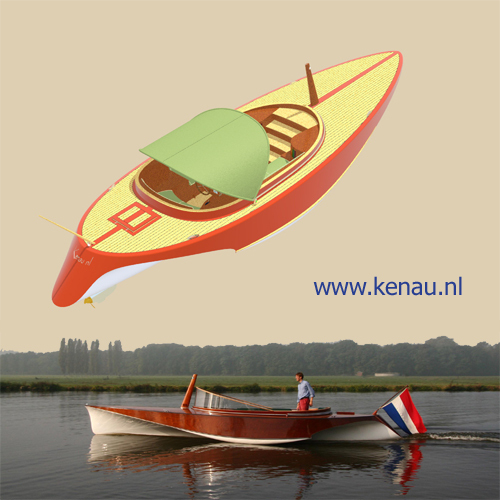
Stuart Wood discussed experience of using Rhino by Heatherwick Studio – a design studio in London, which is well-known for its large-scale projects for private companies and government agencies, such as Routemater - a new double-decker for London:
Unlike existing buses it has three doors and two stairs. Initially the project used AutoCAD, but the 3D-model was designed in Rhino. Presently the model is undergoing testing.
Michael Eden discussed combining digital design with manual production. Michael makes amazingly complex ceramic vases.
What kind of a CAD-conference can nowadays take place without demonstrating the work of a 3D-printer? Rhino UK User Meeting also did not avoid it. Graham Bennett from CRDM, that sells HP Designjet 3D printers in the UK, elaborated on the principles upon which this printer works, and detailed the costs associated with the printer and expendable materials to it. Anyone could witness the magic of 3D printing. HP Designjet printer is nothing else but Stratasys uPrint. Here the idea of badge-engineering worked perfectly: buyers feel confident about the HP brand. In 18 months 220 printers of this model were sold in the UK.
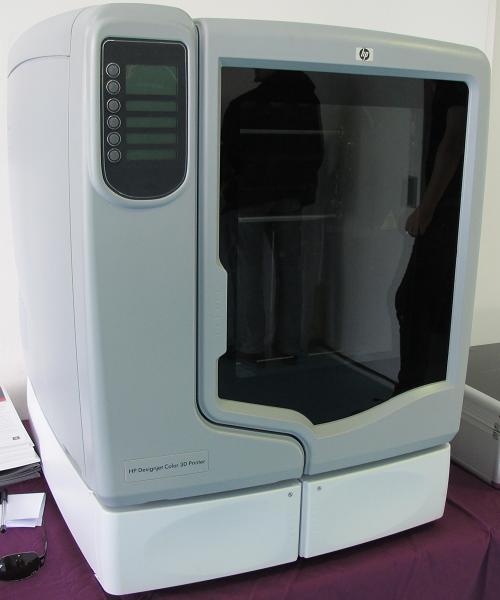
The Meeting ended up with a presentation of new developments in Rhino 5 by Phil Cook, of Simply Rhino. He showed how Shell – a new command works, and demonstrated improvements in the Sweep command. According to Phil, typically the Project command produces very complex curves on the surface – with considerable number of control points. Now it has an option enabling to simplify the projection. A virtual manipulator Gumball is an important new feature in Rhino 5. By clicking twice on one of its arrows, users can enter a particular value, for which an object must be shifted along a relevant axis. In conclusion, Phil Cook demonstrated new visualization tools.
Closing the Meeting, Paul Cowell thanked all presenters for coming up to London and told us about the www.rhino3d.co.uk website, where it is already possible to find several educational videos demonstrating new functions of Rhino 5.
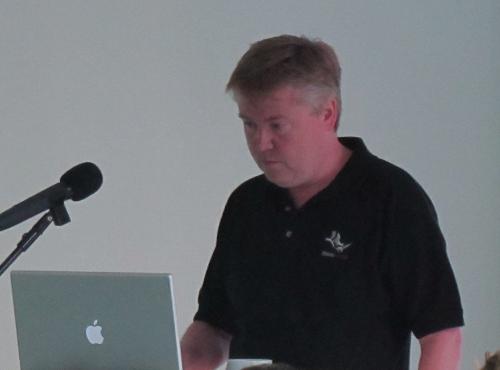
Leaving the Museum and admiring a magnificent view of the Tower Bridge (the Design Museum is located on an embankment very near to this London sight), I made an effort to sum up my impressions from the Meeting. Clearly, the novelties of the 5th version coupled with the new (or considerably updated) plug-ins - T-Splines, VSR Shape Modeling, RhinoWorks and Scan&Solve, transfer the old good Rhino into a powerful platform, threatening to take the positions of mid- and high-end design systems. For considerably less money users get a fundamentally better functional: advanced techniques for free-form surface modeling, convenient parameterization and automated express-analysis. Users of, for example, SolidWorks can’t even dream about this. Does it mean that Rhino 3D has a chance to become the most popular 3D design system? It’s rather difficult to say: after all, the sizes of the companies are not comparable (RMA staff is a two-digit number, and RMA is not backed up by a multi-billion corporation). Besides, plug-in developers are disengaged, often duplicate the functional, and what is the most important, they have their own vision of the market niches for Rhino, each developer pursuing an independent marketing policy. Until Seattle takes reins, Rhino will remain a platform widely popular in privy and driven mainly by the enthusiasm of its users and third-party developers. Still, it is common knowledge that all rhino species have poor eyesight. But has this minor fault even been a problem for any of them?
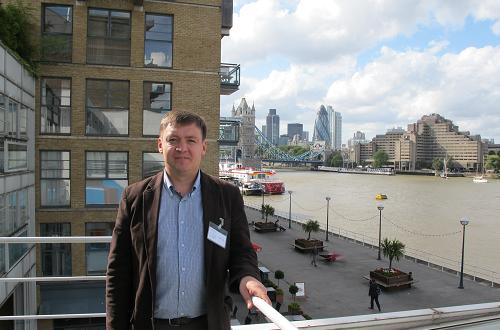
Permanent link :: http://isicad.net/articles.php?article_num=14519
|
 |