Articles
10 Jun 2013 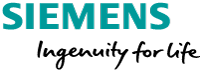
Siemens PLM Software: “In Russia we work with customers who want to be leaders"Interview with Ñhuck Grindstaff, President and CEO, Siemens PLM Software, and Victor Bespalov, Vice-President and CEO, Siemens PLM Software, Russia and CIS
The annual Siemens PLM Connection 2013 forum was held in Moscow Business School SKOLKOVO on May 21 and 22, 2013. Dmitry Ushakov visited the event and used a unique opportunity to interview Chuck Grindstaff and Victor Bespalov. A short but condensed conversation covered several topics like 2D vs. 3D, synchronous technology, and comparison with main competitors on CAD and PLM market.
Mr. Grindstaff, you are untypical CEO for a large CAD vendor: your have background in R&D rather then in sales. Does it help you to manage such a large business?
Chuck Grindstaff (CG): My background is not in R&D only. As an entrepreneur I was also a manufacturer. I made electronics and then I sold this business.
You mentioned “rather than sales”. I think any general executive, any CEO is a multi-disciplinary individual. The strategy of the company as it is close to me is the combination of organizational development, market development and product development. I spent a good deal of time, more than 60% of my time with customers. I would not call it precisely “sales”. I am generally not in the first line of defense for negotiating the price of a contract.
On the other hand, my business background and my personal background such that it is, is typical for any other large engagements to make sure that my vision and customers’ vision are aligned. And frankly it is an important part of sales process.
So I think I wouldn’t change background, I think it is the right background for this industry.
Siemens AG acquired a lot of engineering software assets during last years. Which of them do you manage now in Siemens PLM Software? How do you position them?
CG: I look after the Siemens PLM Software components – this is NX, Teamcenter, Tecnomatix, and all Velocity products including Solid Edge. These are all the traditional products of UGS. In the last year and a half we also bought Vistagy, Perfect Costing Solutions, Kineo CAM, as well as LMS. And these are all in my global responsibility. My software focus is on helping customers design products, manufacture them, and then execute.
You do mention that Siemens has invested a lot in software. Actually over the last seven years a significant sum was invested
Many engineers still design in 2D. Do you see a barrier when moving from 2D to 3D for them – due to different design methodology implemented in different products? What is your strategy here to help users to move from 2D to 3D? Do you propose a unified 2D/3D environment to your users?
CG: This is true – many engineers still work in 2D. Is there a barrier moving from 2D to 3D? I guess what I would say is design is from very beginning the idea of balancing requirements, balancing what’s possible from physical point of view, from material point of view, from performance, cost – all these are important. It is not unusual for early stages of the design to be done what we call even one-dimensional model - just mathematical model of the functions of a product.
2D design can be very effective when most of the design criteria is representable in 2D. So give you an example of a turned part with rotational symmetry. Most of the geometry is defined by supplied 2D profile. And obviously from that one can extrapolate to 3D properties such as stress, strains and overall characteristics of the part. There is nothing wrong with these simple design methods to accomplish the process of balancing requirements.
Probably the real nature of your question goes beyond that. When people are still using 2D techniques where there are complex 3D interactions, they need to reason all these interactions mentally rather than as computer assets.
Frankly I think the barrier is still mainly institutional process and not technology or productivity one. And maybe there are some documentation requirements; for example it is not untypical to have a drawing requirement, and maybe a designer completes his design most efficiently directly on the drafting board.
When I started in this business 35 years ago, this was a question, which made much, much progress. And I think most real complex machine problems, packaging problems, that phone (pointing at iPhone) have to be done in 3D in order to really prove the design and for manufacturing.
So what I would say is some problems still make sense in 2D because of the nature of the problem, but in those problems where 3D is the obvious choice, the real problem is that people maybe don’t have the right system, maybe they have not enough investments, but technologies now work. We can model anything in 3D.
Victor Bespalov (VB): Maybe I’ll add some words on the subject. I completely agree with Chuck, and the most interesting is that today there are no legal barriers to accept 3D model as the main source of information.
Leading Russian companies, such as United Aircraft Corporation, United Engine Corporation, move in the direction of making 3D model the main source of information, including certification tasks. Drawings are mainly used only as simplifies views to sign physically.
One more our customer, who is now actively moving in that direction, is KAMAZ, doing a very large work with the Russian Ministry of Defense to negotiate a list of documents to be produced from 3D model to guarantee the customer required level of quality and design changes.
One more time: from legal point of view, from technology point of view there are no barriers.
CG: I should say because maybe your readers are rather technical in nature. Consider things like manufacturing instructions, PMI, formal positioning tolerances, all of the characteristics necessary for actual manufacturing and inspection, which traditionally are delivered on a drawing-based environment. We believe as Victor said that it is now technologically solved issue in 3D and I think that well it’s possible but still is a mental process barrier for some people. Of course if you use a 3D model you can do automatically CNC programming, if you have a drawing it is not automatic anymore.
Part of my question was: do you help and how do you help your customers to move from 2D to 3D? Do they need your help?
CG: Well the best thing to really answer the question will be to sit down with our experts and show how our NX products can do 2D design seamlessly with 3D. We can interoperate from 2D to 3D, from surfaces to solids, we unite the separate distinct worlds.
And to be frank, we invest still in 2D design. You have also a question on synchronous technology; we have just done a significant amount of work in applying synchronous technology computational model to 2D design processes.
VB: We help also in the following way. In most cases we deal with customers considering drawings as the main source of information. It is not a problem for us to train people, designers and manufacturers, to use 3D. Because all our trainings target this goal. The real problem consists in changing the customer’s normative legal base – to define that the main source of information is 3D model, not drawings. Main problems here are organizational, and we help to solve them. Today we come to our customers not only with technologies, but also with document patterns, which may form the normative legal base of 3D model as the main source of information.
How do you see existing and future applications of synchronous technology: is it for solving niche problems (like editing imported geometry) or it is a fully functional replacement of traditional history-based parametric modeling? What was the reason of your recent decision to release synchronous technology as a separate application (3DSync)?
CG: We don’t see synchronous technology being a strict replacement for history-based modeling for many, many aspects of the design, that are the benefits from recording the specific relationships between things, the specific way to represent those constraints in a persistent fashion and we appreciate them, and want continue to drive our systems to perform to be capable in this area.
We also think that the history approach can be confining for design, because the approach to the constraints system where relevant dimensions are included, may also include - by accident - other constraints. And this is where synchronous technology can really work well because we can on the fly reassemble, reconfigure the constraint system and solve simultaneously.
The other thing to think about is in history modeling you have the complex history tree. The last feature on the tree wins a battle against all the other work you have done. So engineering work done upon the tree can be invalidated down the tree. And this is an issue. History has the problem of release-to-release compatibility. It has the problem of interoperability with other systems. So there are many places where history - while solving very important problems - also represents a boundary for other applications. So to sharing data having the NX system talk to a Pro/E system, it’s not so simple.
So our invention of synchronous technology is intended to deal with the problems of interoperability, data protection, design change, response to a particular set of constraints that are unique to a problem, and performance. And we do this in a relatively special way and we’ll continue to invest. And 3DSync is a package solution to solve these niche problems. If somebody maybe even does not use our core CAD product, but still has this problem of importing the suppliers’ generated data from a foreign system for modification, 3DSync is an inexpensive way to accomplish that. So it’s a packaging concept.
Siemens AG has never published financial results of Siemens PLM Software. Could you share some figures with us – if not absolute sales, then their dynamics? Can you compare your growth rate with your main competitors – Dassault Systemes, PTC, and Autodesk?
CG: Yes we do not publish our results, and you know reason of that. It is not because of hiding anything, but since Siemens is a hundred billion dollar incorporation with many, many business units, and if every business unit will make its public data regarding our financials, releasing by accident a conflicting message to the capital markets. So we choose not to confuse people so that all things happen in a way, which is predictable and something that the analysts and market players can use.
We do know where our growth is rooted to competitors. Our organic growth rate is the best in the industry. Our core business had grown over last several years ahead of the peers. And now the acquisitions we have added increase the total growth.
So when you look at these other guys, Dassault and PTC and Autodesk… Looking at their organic growth, you can be assured that our organic growth is superior to these companies. And then you have some data points of acquisitions we published to get an idea of that contribution.
And in the terms of total turnover we are bigger than PTC and a little bit smaller than Dassault. (After a pause, smiling) For now.
This is not your first visit to Russia. What does the Russian market mean for Siemens PLM Software? What is Siemens PLM Software for Russian market? Do you outsource your R&D activity to Russian software development companies?
CG: This is not my first visit to Russia. Luckily I came back several times. The Russian market is actually quite significant market to us. And it is a market where we have a high growth rate and the customers we do, thanks to the team. All we have been able to develop over the last few years is a set of accounts where the future of the design process is not a following strategy, but a leading strategy. You know Victor told about specific enhancements that we have done for the Russian market. We think several of the customers who work with us can not only help us to customize and localize for the Russian market – they can help to drive process around their entire work.
You talked about synchronous technology; maybe you also saw my speech I did about 4GD (4th Generation Design). Both of these technologies enable completely new and fresh ways to work. In my opinion there are several Russian companies with innovation inside that can help us to refine these technologies over time and build them into the processes.
And no, we don’t typically outsource our R&D to Russian software developers. We would, but we have our own developers in house. We don’t normally outsource much of our R&D. The most costly is documentation and it is typically an Indian operation or a Chinese operation. But there is no reason other than history that we haven’t used a lot of Russian service providers.
Thank you very much for this interview!
See also:
Permanent link :: http://isicad.net/articles.php?article_num=16184
|